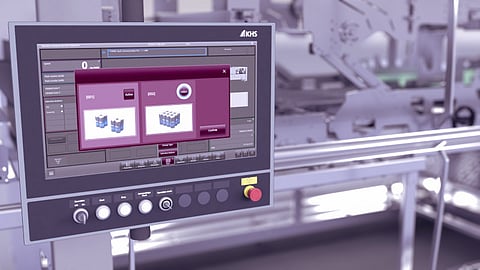
More efficiency, speed and reliability in the packaging process for beverage cans: KHS is automating the product feeding and formatting of its Innopack Advanced series packaging systems and Innopal PB palletizers with robot grouping. Compared to manual format changes, a much faster and easier changeover to new products is achieved. This means that time savings of up to 30 minutes can be achieved per format changeover. At the same time, reproducibility is increased by constant adjustment accuracy when changing.
Against the backdrop of dynamic developments in the beverage industry, bottlers' requirements for fast response times when adapting primary and secondary packaging are growing. At the same time, the complexity of packaging machines is increasing due to extended adjustment options and the use of format parts is increasing. "We are meeting these challenges with an automation concept that not only reduces the effort required to convert machines to other products or packaging forms, but also makes them more reliable and efficient," says KHS product manager Ernst van Wickeren.
Higher efficiency in KHS packers
The semi-automated format changeover can be easily implemented with almost all packaging systems in the Innopack Advanced series. In their development, the KHS experts initially concentrated on the product feed and formatting process modules, which usually require a relatively high level of adjustment on the part of the operator. An example: In the inlet of the machine, the containers are guided through aisles with railings to the packaging. When changing the format, the user has to loosen and adjust 30 to 50 adjustment points of the aisle railings, depending on the diameter of the can. With the concept of semi-automated format changeover, this is done at the push of a button, so that it is only necessary to ensure that there are no containers on the inlet at the time of the change. In addition, the operation of the adjustment units is now motorized and automated. According to van Wickeren, the degree of automation in KHS packaging machines is far from exhausted: "There are still format change parts that require manual replacement. That's why we're working tirelessly on further solutions."
Full automation in palletizing
With the Innopal PB palletizer with robot grouping, KHS has already achieved full automation of the format changeover. "This can now also be done at the push of a button for complex formats," explains Christoph Wiesenack, product manager for palletizing at KHS, "In addition to the automated systems already available, the centering systems in all variants of the Innopal PB series can now be equipped with servo motors." This saves time during the changeover and allows maximum precision when collecting and placing the grouped containers on the pallet. Thanks to the automation of the jaw change of the grouping robots, the adjustment of the width of the slider and the automated adjustment of the guides, no manual intervention within the palletizing machines is necessary. This increases operating safety.
Improved reproducibility
Due to the relief in the dry end and the reduced complexity of the format change, the demands on the operators and the generally required number of employees are reduced. At the same time, KHS minimizes the susceptibility to errors, for example in the form of deviating settings in the course of a shift change at the filler. "The motors always move automatically exactly to the set position, which significantly improves reproducibility," explains van Wickeren. Readjustment can therefore be dispensed with, so that production can continue at full power immediately after a change. In total, the time saved with the help of automation is up to 30 minutes per format change for packing systems and up to 20 minutes for palletizers.
Click HERE to subscribe to our FREE Weekly Newsletter