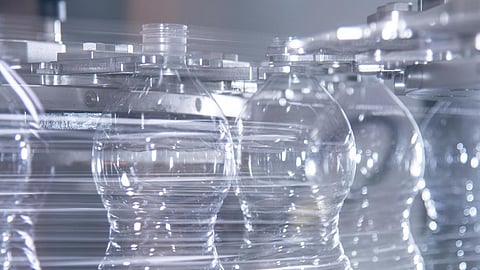
Whether it’s climate change, supplying the world’s population with enough food and drink, or responsible stewardship of packaging materials, humankind is currently facing major challenges which are also impacting the food and beverage industries.
In Krones’ view, PET can help solve some of the pressing issues of our era. After all, this type of packaging can be sustainable – provided, of course, the process for producing the material is resource-economical and a closed cycle is maintained. Besides recyclability, plastics also have further major advantages compared to other types of packaging. They weigh substantially less, which means PET bottles have a significantly lower environmental impact than other materials over lengthy transport distances. What’s more, plastic bottles don’t break. That is a huge advantage for transport in poorer regions, where the traffic infrastructure, for instance, is substandard and access to clean drinking water is only available on a very limited basis. This advantage can help meet one of humankind’s biggest challenges at present: supplying the world’s population with enough food and drink. According to the German Foundation for World Population, approximately 9.74 billion people will live on our planet by 2050. Making sure that all of them are reliably supplied with packaged water is just as important as furnishing them with enough food.
In order to meet the rising demand for packaged water, filling companies need appropriate machine speeds. Contrary to commonly held opinion, a single larger line offers better performance in terms of both energy and media consumption per packaged unit than multiple medium-output lines.
Krones’ response to this development is the wet-end block achieving an output of 100,000 0.5-litre water bottles per hour – thus establishing a new benchmark in block technology.
100,000 water bottles in one hour
The basic production sequence of this 100,000-bph block is just the same as in a conventional ErgoBloc L. But when you take a look at the various individual machines, it soon becomes apparent that there are some key differences.
The preform feed unit passes the PET preforms into the Contiform 3 Speed stretch blow-moulding machine. This machine generation, which was released in 2018, already eliminated the need for a pressure pad to hold the two mould halves together. And with a rating of 2,750 containers per blowing station, it set new benchmarks for output and compressed-air consumption. But in order to raise the total output to 100,000 containers per hour and yet further reduce the machine’s carbon footprint, additional innovations had to be brought into the machine. And that is how some components from the fourth Contiform generation came to be used in this high-performance block.
The link between stretch blow-moulder and filler: the Ergomodul
In order to cope with the very high output of the stretch blow-moulder, some additional, optimised components, functionalities and assemblies were incorporated in the Ergomodul. For example, the two Contiroll stations and the Multireel magazines for label reels feature a new buffer system which keeps the label tension at a constant maximum level, thus offering ideal preconditions for thin label films, a boon for sustainability. Another of the machine’s key features is the “no bottle – no label” function. If a service rejection in the blow-moulder causes a gap in the bottle flow entering the labeller, no label is transferred to the vacuum cylinder and the corresponding vacuum cylinder suction bars are retracted upon reaching the gluing unit. As a result, no label or glue is wasted and any gaps in the container flow no longer affect the efficiency of the line.
Two filling units, two closing units – but only one machine
The filler posed the biggest challenge for the development team because there are physical limits to the standard approach of “bigger carousel equals higher output”. At some point, the masses to be moved and the forces acting on them simply get too big to reliably maintain a stable process. In order to prevent this, the block features two modularised filling units and two modularised closing units. That may sound simple, but was in fact difficult to implement because although the filling/closing of 100,000 bottles per hour is evenly distributed among two units each, these units are still constituent parts of a single integrated block with just one valve rack and one sorting system for closures.
The Modulfill Dual features around 60 filling valves fewer than a one-filler solution would need for the same output. Thanks to its compact size, the filler takes up less space, but its output is still almost 20 percent higher.
Click HERE to subscribe to our FREE Weekly Newsletter