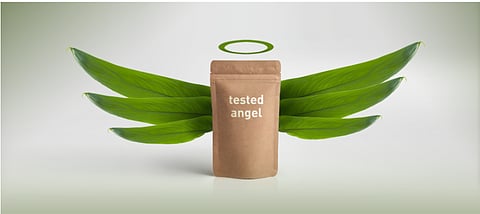
Sustainability is a rising trend across all regions and industries of the world––even in packaging. With consumers increasingly aware of the impact of their purchasing power, many are pushing the drive towards more sustainable consumption, starting with packaging waste. In fact, according to a recent survey among digital-savvy shoppers who are keen to experiment with new brands and products, also known as "empowered consumers," 68% say they plan to step up their efforts to identify brands that reduce environmental impact. In comparison, 61% seek out energy-efficient labels when shopping. This paragraph mentions plastics, but we have edited it, so it's not as strong.
At the same time, consumer pressure is also pushing governments action around the world, for example, regarding the environmental impact of single-use plastic packaging waste. Local and national governments on every continent have started to react to these public concerns, leading to the increased implementation of regulations to improve waste-management processes and minimize environmental waste. For instance, the EU's single-use plastics directive targets eliminating the most common plastic materials found on Europe's beaches was implemented in 2019, among many other similar schemes.
In response to such widespread regulations, many FMCG brands are seeking alternative packaging solutions to keep up with the legislative moves. Meanwhile, since the overwhelming majority of consumers report that they are willing to pay more for sustainable packaging and minimize their footprint, many brands also recognize that these regulations present a new opportunity to draw customers using innovative, eco-friendly alternatives to traditional plastic waste. But first, there is a need for new high-performing machines capable of handling the new generation of packaging materials.
New materials, new requirements
Packaging has been innovated at an unprecedented rate over the past decade, especially in response to the global trend of sustainable consumption. At the same time, however, these new sustainable materials are also causing new challenges for machine manufacturers that are used to dealing with more traditional materials.
On the one hand, new materials are very different from traditional physical and chemical properties. This can result in uncontrolled stretching or sealing when running on horizontal form-fill machines (HFFS) equipment capable of compromising production performances. For example, there are many technical challenges regarding the compatibility of new sustainable materials and their integration with zippers, caps, or spouts. Mono-material films require a lower sealing temperature and are much more sensitive to high degrees, with a narrow sealing window. Contrarily, caps are usually made of materials such as PP and HDPE, which require higher sealing temperatures.
Aside from testing the functionality of the packaging, it is important that new materials are also thoroughly tested with existing machines to prevent downtime of a manufacturer's production line while also ensuring successful sequencing. Most importantly, it's important to know the correct ways of testing, handling, and sealing new materials. That's why two years ago, Volpak's R&D department, together with their technological partners, launched a new center to develop innovative prototypes for this very purpose.
PouchLab: Volpak's thriving R&D center
Luckily, it is now possible to use new materials with confidence thanks to Volpak's center for research, development, and testing of flexible packaging: PouchLab. As a renowned leader in HFFS machines for flexible packaging, Volpak has been devoted to developing solutions that comply with the new global regulations that aim to reduce the impact of packaging on the environment. Established in May 2018, PouchLab has supported customers and partners to optimize and innovate their flexible packaging solutions.
Located in a controlled area within Volpak's headquarters in Barcelona, the PouchLab has also served as a special "R&D Excellence Center." These premises contain dedicated closed boxes for the storage of materials and a state-of-the-art pouch-forming machine based on HFFS technology and complete testing equipment. Many materials and tools can be rented by Volpak customers to analyze their material, make pouches and test the quality of the product: this includes a tool to measure accurate electrostatic charge, a 3d printer for rapid prototyping, a stress test machine, a powerful microscope to analyze seal quality, and a high-speed camera to investigate machinery issues.
Since its inception, the center has also been helping brand owners who need to set standards for their packaging, from enhancing the size of the pouch line to downgauging the packaging and, most importantly, the exploration of new materials. With PouchLab, customers can measure the film stretch of their material and control and monitor seal temperature, seal pressure, and seal time while also supervising film tension.
Several Volpak machines are already handling recyclable pouches of different sustainable materials, including paper and mono-material plastic. To make this possible for an increasing number of customers intending to use a wide range of materials, Volpak establishes partnerships with film suppliers and other key stakeholders involved in the pouch production process. It is thanks to such collaborations and efforts that, over the last two years, PouchLab has played a primary role in developing the paper-proof technologies that are now available on many Volpak machines, making these one of the few "100% sustainable" solutions in the field of flexible packaging. What's more, 90% of films tested in PouchLab are made with sustainable PE material, which is becoming the standard worldwide.
In addition to Volpak customers, PouchLab is also intended to function as a research center for industry players such as manufacturers of film converters, caps and zippers, and technological centers and suppliers of raw materials. All could benefit from the lab's multiple offerings, for example, to compare the behavior of different structures, as well as to test machinability, double-check the performance of film materials, and develop new sustainable solutions for flexible packaging.
As PouchLab celebrates the end of its second year, the center will continue to partner with suppliers and manufacturers to meet even greater technical challenges for a more sustainable future.