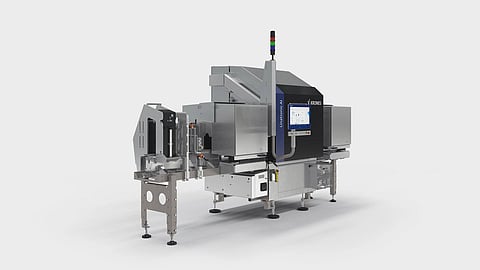
Krones made a quantum leap in inspection technology two years ago with the development of Linatronic AI. For the first time, an inspection machine used deep-learning software for automatic detection and classification of damage and contamination – with great success: Linatronic AI can distinguish between anomalies and, for instance, water droplets with a reliability rate of 99.9 percent. These high marks are only possible because the system uses deep-learning technology based on an artificial neural network. Linatronic AI is now in service and proving its capabilities daily in several breweries – reliably detecting defects that had previously gone unnoticed or are simply invisible to the human eye.
Better detection of hairline cracks
Whenever glass bottles are processed, there is a risk of the glass chipping or breaking and, thus, of glass fragments being released. Breakage is usually caused by undetected hairline cracks in the material that are not visible to the naked eye, which is not able to withstand temperature fluctuations or the pressure of beverage filling. As a result, glass fragments can fly, though various safety measures prevent injury to operating personnel.
There are many reasons such cracks arise. Damage can occur at any point in the lifecycle, be it in the consumer’s possession transport, or production. Bottles with crowns are also susceptible to hairline cracks at the neck finish, resulting in chipping or even complete breakage on the neck finish.
For this reason, it would be best if bottles with any existing damage never even make it to the filler. And the Linatronic AI software helps accomplish just that. Improved base-chip detection means fewer damaged bottles fed into the filler, and the potential for shards flying is almost eliminated.
Besides detecting hairline cracks, Linatronic AI also does a better job of registering chips on the sides of the neck finish and the wall. The base inspection unit is programmed for improved glass fragment detection without the need for an additional x-ray camera unit.
The software does not need to be installed by Krones technicians onsite because Linatronic AI can use a single neural network for all customers using the same bottles, so no customer-specific parameterization is necessary.
Impressive inspection results
Since its market launch, Linatronic AI has been operating in several breweries. “I was a bit skeptical at first. I thought: Is that necessary?” recalls Johannes Kagerbauer, bottling hall manager, Gräfliches Hofbrauhaus Freising. “We’d been using a Linatronic before and had always been satisfied with its performance.” But Linatronic AI impressed him through and through, with a precision that far out-performed conventional inspectors. “It won me over. I can view the error photos on the machine. And so far, I haven’t found a single one where I’d have said: This bottle should not have been rejected. And when it comes to identifying base chippings, this inspector is also much more accurate and thus instrumental in minimizing burst bottles at the filler.”
And that impacts overall equipment effectiveness (OEE) and total cost of ownership (TCO): By preventing false rejects, Linatronic AI can leverage massive potential for cost savings. Not only because water droplets, color streaking, overpressed neck finish, or out-of-round bottles no longer result in an automatic rejection of the container but also because it obviates the need for the neck-finish blower.
Click HERE to subscribe to our FREE Weekly Newsletter