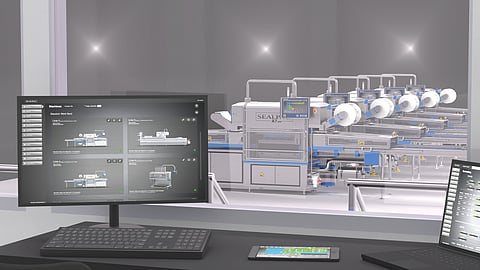
SEALPAC’s high-output traysealers and thermoformers are fully prepared for Industry 4.0 environments. Equipped with innovative production data recording, they support end users by increasing the efficiency of their lines through permanent data analysis in real time, by reacting quickly and flexibly to changing requirements, by detecting errors immediately, and by optimally controlling their resource management.
Comprehensive data recording
SEALPAC’s fully automated traysealers and thermoformers are easily integrated into line control software, for example by using OPC/UA. As such, they provide the end users with a detailed and systematic collection of their operating data in real time. By doing so, SEALPAC supports the line control software used to record comprehensive data for each connected piece of equipment, such as the status of operation, maintenance requirements, machine settings, and stops carried out. In addition, it allows for a complete overview of the line performance, errors occurred, and program changes by operators. The ability to measure the cycle count of individual tools, which are used on different traysealers, is one of SEALPAC’s special features.
Transparent production environment
The data provided by the traysealers and thermoformers can be made available in a variety of reports for further evaluation. This supports companies, both in food and nonfood segments, by increasing their productivity, making their packaging process more efficient, and improving their planning capabilities. With the information provided, maintenance on the production line, such as for the SEALPAC machines and tools, can be planned according to specified intervals. Detailed analysis makes it possible to compare the productivity of lines with one another, whereas the various error evaluation options help to eliminate weak points. Overall, the complete documentation of data and its representation in real time will support those responsible in planning their processes even better, counteracting possible production disruptions in advance, further improving the line’s availability, and exploiting optimization potential.
Click HERE to subscribe to our FREE Weekly Newsletter