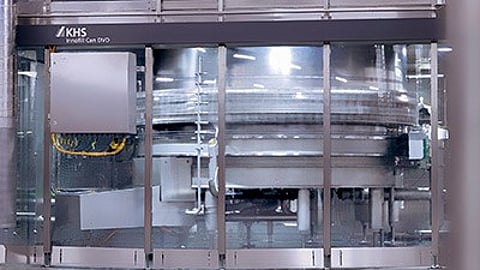
With what is now its third canning line from KHS, RHODIUS is doubling its capacity in this container segment. Despite difficult conditions, the mineral water and contract bottler continues to rely on a clear growth strategy – for itself and for its customers. The optimization of the returnable glass line installed in 2020 also contributes to this.
The beverage can has a long tradition in the Brohl Valley in Rhineland-Palatinate: as early as 1977, RHODIUS Mineralquellen und Getränke GmbH & Co. KG was the first mineral spring in Europe to fill its water into tinplate containers here – on a system from the Dortmund-based system provider KHS. Still a real pioneering feat at the time, the investment sets the course for a success story that has lasted for more than 25 years.
With the introduction of the deposit on cans in Germany in 2003, the market collapsed completely. Unlike many competitors, the company, which has since become the market leader in the can sector, decides to continue to place its trust in the segment and the technology. In order to improve the utilization of its now little-used capacities, RHODIUS is focusing on contract filling. Within a few years, the initial losses can be compensated, with the share of contract orders contributing to total output gradually growing to a total of around 50 percent – and even to around 90 percent in the can sector. Large brands as well as small ones are bottled here, so that the customer base is highly fragmented with almost 100 companies. The same applies to the range, which includes a total of more than 150 different products. In 2016, a second KHS line with a capacity of up to 50,000 cans per hour will be installed to meet the growing demand. Flexibility and hygiene are very important here: After all, the frequent product and format changes on the two can lines should be as efficient as possible in terms of filling and outer packaging.
With its growth strategy, RHODIUS will continue to focus entirely on beverage cans: at the beginning of 2023, the family-owned company will invest around 15 million euros in doubling its capacity with a third KHS line: a total of up to 200,000 containers per hour can now be filled – up to 1 billion cans per year. "We have grown very strongly with our customers," explains managing partner Hannes Tack. "Today, we produce around the clock, every day of the week. Our goal is to enable our customers to grow in the future." To ensure that they benefit comprehensively from the expertise accumulated at RHODIUS and receive the best possible support, a separate sales and service team has been formed in Burgbrohl to deal exclusively with the needs of contract customers. Positioned as a "Can Filling Experts", the company consistently plays its trump cards under the motto "CANformation", for example at the annual customer event "Can Day" when it comes to technology, product quality and diversity or sustainability.
In the course of planning and realizing the latest investment, a whole series of challenges arise. One of the biggest concerns the spatial conditions at the company's site, which cannot be expanded at will in the narrow Brohl Valley: "A dark, old room was available for the new system, in which a decommissioned glass line had to be dismantled before the hall could be renovated," says Gerd Bodenheimer, senior sales manager at KHS, recalling the start of the project. "Since we have to use every centimeter up to the ceiling in the empty can area, we relied on our innovative 3D planning right from the start – even during the quotation phase." For this purpose, laser scans of the existing building fabric are created in order to be able to capture the actual situation as accurately as possible. "One advantage of this method is that we have greater planning security, because everything that interferes or gets in the way can already be taken into account in the three-dimensional layout – in this case, for example, a support around which we had to plan and build the palletizing system. The most important thing, however, is that with the help of 3D system planning, we can check the ergonomics and operating concept of the machines together with the operators at an early stage in order to enable a smooth process later on." The fact that the finished packs are then transported two floors up two floors for palletizing by means of two spiral conveyors over a height of nine meters is just one of many other details.
In addition to the huge variety of products and packaging, other challenges included the high quality requirements as well as the ecological and economic sustainability goals of the new line. KHS offers solutions for each of these aspects to provide the flexibility, quality and performance that RHODIUS needs in view of its ambitious goals. "The new line can handle up to 99,000 cans per hour – twice as much as our previous systems, but with the same amount of personnel. Of course, this makes it much more efficient and helps us to counteract the cost increases we are currently facing in Germany," Tack emphasizes.
"The system meets our special hygiene requirements on the one hand through the hygiene room in the area of the filler-capper unit and on the other hand with a double flush with gravity and vacuum drum rinsers - this gives us the certainty that the containers are really clean before they are filled."
One feature that particularly excites the eighth-generation entrepreneur in the family is the alcohol module built into the blender, which KHS offers as an option for new machines. This development makes it possible to add high-proof alcohol to beverages directly in the blender. This greatly relieves the syrup room, in which alcohol-containing products previously had to be mixed. This process requires a certain amount of manual work and carries the risk of inaccurate measurement results at the end of the mixing process, especially in the higher percentage range. "The alcohol module makes the line very interesting from a technical point of view," says Tack, explaining: "It gives us a consistently high quality, which is made possible by exact measured values recorded at intervals of 10 seconds or automatically corrected in the event of the smallest deviations." If, like RHODIUS, you also bottle high-proof mixed drinks, for example for the African market, this is particularly important.
As a beverage manufacturer that already produces in a climate-neutral way, the long-established company focuses on energy efficiency, which offers ecological as well as economic advantages, as Tack emphasizes: "Sustainability plays a central role for us. That's why we make sure that our investments use technologies that consume as little energy as possible. From this point of view, the KHS line is state-of-the-art – especially in energy-intensive machines such as the pasteurizer or the filler/capper unit."
Finally, when it comes to secondary packaging, the system also leaves nothing to be desired. "Whether it's the mixing of the beverages themselves or the variety of packaging that our customers demand, we don't shy away from complexity," Tack clarifies. This is hardly surprising, given that the fully automatic and modular Innopack Kisters WSP packaging machine provides him with technical equipment that sets no limits to even the widest range of variants: from cardboard to trays and shrink film to wraparound cartons, in which the container is enclosed by cardboard. The latter is particularly relevant for export because it provides good all-round protection for the sensitive containers. Despite all the flexibility, the dry end in particular was planned together with KHS in such a way that even more possibilities can be exploited in the future: "We are always open to new ideas," says Tack. "The layout allows the integration of up to two additional packers." Conceivable, for example, would be the Nature MultiPack, which combines beverage cans into a pack using only adhesive dots, or the "TopClip", an attachment made of cardboard. More and more of its customers, as well as end users, attached importance to reducing packaging material, especially plastic film.
From the packer, the multipacks go to the palletizing center, where they are assembled into palletizable layers with the help of two Innopal RG robots. These are stacked by a space-saving Innopal PB-HS palletizer so that they can then be packed safely for transport. Here, by the way, the output of all three canning lines runs via a belt control system with direct acceptance to a common speedloader system. "This requires both sophisticated logic and a solid physical connection," explains Tack. "KHS has mastered both very well." From the production plant, the goods go to the logistics plant in the center of the village, which has also long since reached its spatial limits. Remedy is in sight: The new logistics center with a hall and office space of almost 2023,25 square meters and direct motorway access will be completed by autumn 000.
How can the significant investments be reconciled with the current tense economic situation? Tack admits that in view of the Russian war of aggression against Ukraine, the overall economic situation has deteriorated and purchasing power is declining compared to the previous year due to inflation. In the long term, however, he expects the successful course to continue. He has already been right in his confidence in the past: "The pandemic and the associated repeated lockdowns did not have a negative impact on overall demand. On the contrary, sales in the food retail sector have really boomed."
However, when far-reaching expansion decisions are pending, the 40-year-old does not rely on his gut feeling: "For us, it is essential that we pursue a well-prepared strategy that we verify and question both internally and externally. In addition to our own know-how, we use that of our customers. And we have an advisory board with which we discuss major investments." Nevertheless, there is no one hundred percent guarantee of success, so that in the end a certain amount of luck is always required.
Tack describes the trust, reliability and authenticity of the relationship with technology partner KHS as one of the basic conditions for the success of new projects. "We have been working together in a very cooperative and solution-oriented manner for many years and can discuss all challenges openly and at eye level. As a result, we feel understood as customers and that our needs are taken seriously." Of course, this includes the fact that there are sometimes less pleasant topics that need to be clarified. In addition, Tack thinks of the global supply chain bottlenecks, which affected the new line in terms of time, despite all KHS's efforts to find alternative solutions. Conversely, it is the enjoyable shared experiences that create a special connection – for example, when, at the end of months of project collaboration, the new canning line shines with a purchase rate of 95 percent in the first test.
However, RHODIUS and KHS are not only working together successfully in the can segment, there is also great satisfaction with the returnable glass line also installed in Burgbrohl in 2020. The mineral spring fills and packs up to 20,000 containers per hour in many different formats and crates on the line. At the same time, RHODIUS serves a wide variety of products. "This enormous range of processed formats, containers and products makes the glass line very complex," explains Roger Schwarz, line optimization auditor at KHS. "That's why it makes sense to audit the line regularly and comprehensively. As a reliable service partner, RHODIUS commissioned us with this task at the end of 2022."
As part of the line audit, the four-person KHS team included all components, including machines from third-party suppliers, in its overall assessment. To this end, the specialists from the Dortmund-based system provider worked closely with the employees of RHODIUS and the manufacturer of the inspection and labelling technology on site. Within just 3 weeks, the team analyzed the line holistically. The resulting list of measures served as the basis for the optimization work. In the course of the next few months, among other things, the format-dependent control programming of the infeed belts and the format-dependent settings of the aisle plates on the packer were improved. "As a result, we were able to increase the overall equipment effectiveness for all formats, and we even managed to increase the 0.75-litre mineral water bottle by 10 percent," said Marcus Müller, Technical Manager of the Reusable System at RHODIUS, confirming the successes. Further line audits of the mineral spring should not be long in coming with this meaningful result.
For decades, a historically grown, close partnership has connected the beverage bottler from the Vulkaneifel with the plant and machine manufacturer from Dortmund. Launched in the seventies with the first KHS canning line, RHODIUS now has three of them, as well as a PET, a keg, a BIB line and a returnable glass line. Relying essentially on a technology partner is a strategic decision: "KHS convinces us when it comes to project planning, installation and commissioning," says Hannes Tack, Managing Director of RHODIUS. "And KHS ensures maximum system availability during operation. In addition, the focus on one supplier simplifies the day-to-day work of our technical staff, for example through uniform user interfaces, similar functions of the machines or the provision of spare parts." The fact that the contact persons have known each other for years greatly simplifies communication and ensures that the system provider is exactly familiar with the needs and requirements of RHODIUS.
Conversely, KHS also benefits from its proximity to the bottler: "Together with such an innovative customer, we can break new ground," explains Senior Sales Manager Gerd Bodenheimer of KHS. "For us, RHODIUS is almost like a 'playground' where we can test and further develop prototypes." Added to this is the geographical proximity: Burgbrohl is located almost exactly in the middle between four of the five German KHS plants in Dortmund, Bad Kreuznach, Kleve and Worms: If you want to present a reference project to other beverage manufacturers at the flagship customer, the distance is not far.
Click HERE to subscribe to our FREE Weekly Newsletter