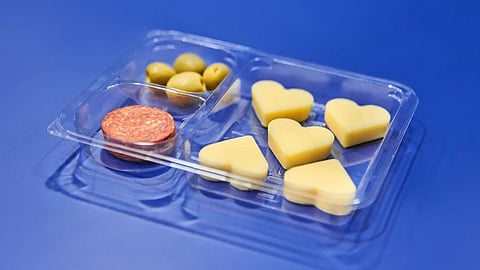
In the area of sliced products in particular, Weber has reached a leading position in the food industry with its integrated processing and packaging lines. But today, Weber is synonymous with much more than that. In recent years, their portfolio has been continuously expanded with solutions for other product and market segments. Handheld goods, snacks, meal assemblies and convenience products like pizza, sandwiches and ready meals, fish applications, baked goods – Weber stands for the development and provision of innovative solutions for automating and processing fresh, perishable foods. Their expertise is evidenced by countless successful customer projects and by the exhibits at the company’s stand at the IFFA. One of the highlights among those exhibits: an innovative automation concept for producing meal assembly products demonstrated by the example of a special set-up for assembling snack trays with cheese pieces, sliced mini salami and olives in olive oil. Where other systems have limitations, this unique automation solution allows producers to implement applications and requirements that could not otherwise be realized – automation and flexibility at its best.
Looking at the layout of this line concept, we see that the configuration consists of two independent Weber weSHUTTLE rings that prepare and process the different products needed for this snack tray application. The first ring starts with a Weber Slicer 305, which precisely slices small snack salamis on two tracks and positions them in stacks on two tracks as well, immediately followed by a Weber weSLICE 4000 circular blade slicer that cuts cheese bits, also on two tracks. Both slicers are perfectly suited to the efficient production of medium outputs and offer the highest flexibility for the implementation of many applications in highly compact spaces. With the Weber ShuttleLoader, two parallel weSHUTTLE portion carriers are automatically loaded with the cheese pieces and mini salami portions cut previously. The ShuttleLoader can automatically correct the lateral portion position, which increases process reliability and makes manual intervention to adjust the portions unnecessary. The portion carriers can be individually adjusted depending on the product and application.
The linking and realization of these various process steps in a very small space is made possible by the core section of this creative processing solution: the incredibly versatile Weber weSHUTTLE transport system. The latest generation of the system was introduced during the IFFA. With maximum flexibility in terms of application variety and spatial configuration, line solutions centered around the weSHUTTLE can be tailored to each customer’s specific conditions and needs. The individual track layout is a real game-changer when it comes to integrating new production lines into existing, limited production spaces. This not only saves valuable space but also money, as customers can use the full capacity of their production area on a minimized floor plan. Additionally, the weSHUTTLE contributes to greater food safety thanks to the high degree of automation. Due to the reduction in human intervention in the production process and the hygienic advantages of the system, better hygiene and longer product shelf lives are achieved. Intermediate cleaning of the line is quickly and easily possible, because the portion carriers can be removed in no time and without tools. As an option, a UVC disinfection can be integrated compactly into the system. This automatically and continuously disinfects the portion carriers, significantly contributing to product safety.
Next, the two loaded portion carriers move to a Weber wePICK, which connects the two shuttle rings. The punching station for the cheese hearts, which can also produce a variety of other shapes and geometries, is in the infeed area of the pick robot. It requires no additional space, as it is entirely integrated into the Weber wePICK. First, the cheese pieces are fed through an alignment station that precisely positions before cutting. Then, the cheese pieces are cleanly shaped into the desired geometry with the help of the appropriate cutting method such as a wire of knife cutter – for a precise appearance in every package. The finished cheese hearts and mini salami stacks on the weSHUTTLE portion carriers are then gripped precisely by the wePICK and placed into the trays. The empty trays are located on portion carriers within the second shuttle ring, which is also fed through the pick robot cell. This process of placing the cheese hearts into the packaging is so gentle that no heart ever slides out of place and the cheese is presented in a visually pleasing way.
Within the second shuttle ring, the trays filled with cheese hearts and mini salami are transported to a multihead scale which adds the olives to the snack tray. After that, the filled trays are weighed. The special feature: The control scale is integrated into the shuttle ring so it needs no extra space. The determined portion weight is transmitted to the olive oil dispenser, which tops the tray with exactly the amount of oil required to reach the desired total weight. At the end of the process chain, a Weber wePICK transfers the fully loaded tray to a packaging station, in this case a traysealer.
Apart from the production of special geometry applications with active punching stations, this Weber line can also produce classic applications like sliced meat shingles or stacks. This is a major economic advantage for producers of seasonal products, as the production of seasonal items like punched Santas or Easter Bunnies does not require a separate line that only runs certain times. Since the punching station can simply be deactivated, the line can produce any other desired application outside of seasonal business. This is the ultimate flexibility and added value that can be achieved in just one production line.
With this automation concept, there is nothing to limit the creativity of food processing operations: Other products can also be inserted and flexibly transported with the weSHUTTLE transport system any way the customer requires. The Weber weSHUTTLE is ideally suited for the economic, flexible, and highly automated production of sliced-product variety packs or convenience products such as sandwiches, the automatic filling of all kinds of ready meals, as well as the automatic application of pizza toppings. Customers benefit from the highest possible flexibility, as different applications can be run on the same line. And of course, other types of packaging machines, thermoformers for example, can also be integrated into this automation concept, so it is possible to produce a wide range of packaging types.
Click HERE to subscribe to our FREE Weekly Newsletter