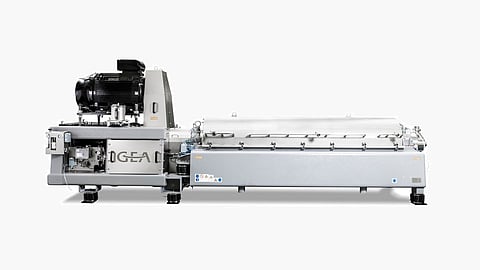
The high energy efficiency, trouble-free operation, modular, compact design, and fast delivery time are the key advantages of GEA decanters in general and in the case of Valmet the CF 8000 decanter.
Photo - GEA
GEA delivers two CF 8000 decanters to ITC Paperboards and Specialty Papers Division in Bhadrachalam, India. The GEA decanters will support ITC's modernization and new construction project.
The Paperboards and Specialty Papers Division of ITC is the leading company in South Asia's paper and board industry. Modern recovery boilers are being installed at the site to improve the ash handling process. Two new CF 8000 decanters from GEA are key components of the ash leaching stage of a modern Chemical Recovery Boiler
The modern chemical recovery boilers are an integral part of the pulp recovery process and generate electricity and steam for the entire mill. This project is being carried out by Valmet, the world's leading developer and supplier of process technologies, automation and services for the pulp, paper and energy industries. Valmet, in turn, had contracted GEA to supply the CF 8000 decanters as part of this overall project.
GEA decanter CF 8000 as immediate and later as a long-term solution
GEA has already delivered the two CF 8000 decanters. They were initially installed in a first step to support the three existing, old recovery boilers. The ash leaching system, including the two CF 8000 decanters, will be connected when the new boiler is ready. The installation of the GEA decanters that has taken place so far is, therefore, initially an interim solution, but one that will allow ITC to continue production without disruption and interruption.
GEA with many years of expertise in decanters and electrostatic precipitators
The decanters were developed by GEA, the world's leading German specialist in centrifuge technology. The technology is based on decades of GEA's market-leading expertise in the chemical sector, with which pioneering processes and technologies for suspension treatment are continuously developed. The key advantages are the high energy efficiency, trouble-free operation, good clarification and dewatering performance, high degree of standardization, modular, compact design, easy integration into established processes with little need for adaptation, and fast delivery time.
Information about the technical background of the project
CF decanters from GEA specially designed for separation and dewatering for chemical and mineral processes
GEA has specifically developed the Flat Pond 6° decanters for clarification and dewatering in chemical and mineral processes. The decanters are made of the duplex steel. A special property of duplex steel is its high corrosion resistance, for example, against surface corrosion, localized corrosion, pitting corrosion and stress corrosion cracking. Due to the high drum speed, solids settle on the inner drum wall and are continuously discharged by the built-in screw conveyor. Due to the comparatively large solids discharge diameter, the 6° shallow pond design results in a significantly higher dry solids content in the solids discharge and thus a high G-force. The decanter centrifuge has special rinsing equipment so that no application-typical solids deposits can form on the solids catcher, in the bowl, on the bowl shell and in the discharge. The entire project consists of the Valmet recovery boiler, the "Valmet AshLeach Duo" and the electrostatic precipitators (ESP). Electrically charged ionic compounds (chlorine, potassium, sodium, sulfates, carbonates) are collected by the electrostatic precipitator from the combustion process, fed into the ash leaching system and mixed with hot water. The valuable ions, such as sodium and sulfate, are returned to the process by the decanters, while undesirable ionic compounds, such as chlorine and potassium are removed. The ash leaching process helps prevent corrosion in the expensive recovery boiler and reduces deposits in the chemical recovery boiler. Corrosion of the boiler would result in immense repair costs. Deposits in the chemical recovery boiler lead to a significant reduction in steam and energy yield.
CF Decanter from GEA as a Game-Changer for Modern Chemical Recovery Boilers
Black liquor is the name for a residue leftover from the chemical pulping process. This residue contains not only wood by-products but also chemicals used in pulp production. The mixture is usually concentrated in an evaporator and then burned in the recovery boiler. The heat generated by this combustion is used to produce steam. Steam is used in the chemical pulping process and paper production, and the excess steam is converted into electrical energy in the turbines.
Ash treatment and ash leaching
Ash produced during combustion in the Chemical Recovery Boiler contains high levels of potassium and chloride. These chlorides increase the risk of corrosion in many parts of the recovery boiler. The potassium also makes the ash sticky, causing it to adhere to internal boiler surfaces and significantly reducing energy efficiency. These problems can be avoided by using appropriate ash treatment systems such as the one used at ITC with the GEA decanters.
Valmet
Valmet is the world's leading developer and supplier of process technologies, automation, and services for the pulp, paper, and energy industries. Valmet's technology offering includes pulp mills, tissue, board, and paper production lines, and power plants for bioenergy production. Valmet's services and automation solutions improve the reliability and performance of customers' processes and increase the effective use of raw materials and energy. Valmet's headquarters are located in Espoo, Finland.