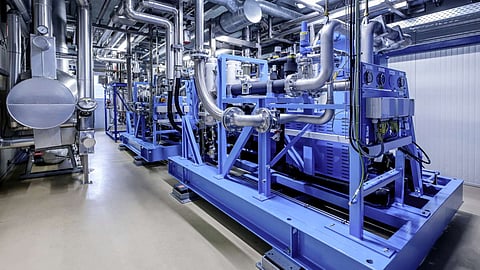
At BrauBeviale 2023, GEA will present its project plans for developing a CO₂ recovery system for smaller breweries with a capacity of 50,000 hectoliters of sales beer per year. These systems collect CO₂ from the fermentation process and make it available as a high-purity resource for in-house production or other applications in the food industry. As a result, CO₂ recovery not only lowers production costs, but also contributes to a more environmentally friendly process with a reduced carbon footprint.
CO₂ supply bottlenecks
While such recovery systems are already established in large breweries, the rising price of carbon dioxide is making CO₂ recovery from in-house fermentation processes an option for smaller companies too. Food-grade carbon dioxide is needed to pressurize vessels before filling and to improve shelf life. In recent years, the CO₂ usually purchased by smaller breweries has become scarce and expensive. “The fertilizer industry, an important CO₂ producer, has been severely slowed down by high energy prices, for example. Some breweries even had to close the taps, because without CO₂, bottling won't work,” explains Klaus Bonfig, head of Utilities in GEA's brewing business. "GEA regards this Craft CO₂ Plant development project as an opportunity to help smaller breweries become more sustainable and autonomous.”
Adapting large systems to smaller breweries
With more than 120 CO₂ recovery plants installed in 35 countries, GEA has extensive experience in configuring these systems. The large-scale plants have a capacity of 100 to 8,000 kilograms of CO₂ per hour and are suitable for breweries producing between 200,000 and 16 million hectoliters of sales beer per year. Now cost-efficient compact systems are planned specifically for breweries with an annual beer output of around 50,000 hectoliters, which process 25 kilograms of CO₂ per hour, which is purified and liquefied with glycol from the central brewery system. The focus of scaling is on simplifying the system. Thus, a special compressor eliminates the need for an additional refrigeration system for liquefaction. All components are skid mounted. These measures contribute to the optimization of operation and also make it easier for breweries to integrate the system into their existing processes. Depending on the CO₂ price, the large systems usually pay for themselves in around three years. The GEA experts also anticipate an attractive return on investment for companies applying a Craft CO₂ Plant.
Click HERE to subscribe to our FREE Weekly Newsletter