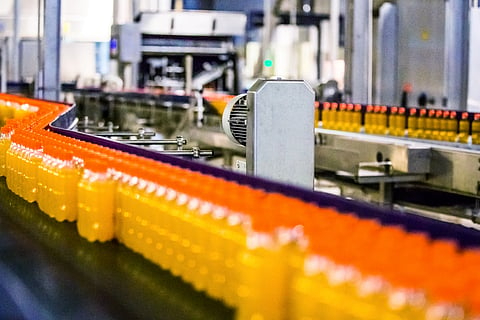
Frozen foods, snacks, ready meals, flavored drinks, and meat, the list of processed foods is endless. Food processing around the world is at an all-time high. Local and international businesses are expanding their storage and inventory management capabilities to handle the vast amount of food being produced, packaged, and transported. This has led to the increased importance of loading and unloading heavy cartons, delivering ingredients to production lines, and movement of food products safely within the facility. Such big operations demand enhanced cost savings and the safety of food products. The solution has come in the form of material handling.
Material handling covers a host of activities, including the movement, storage, protection, and control of materials and products during manufacturing, warehousing, distribution, consumption, and disposal. It covers a range of manual, semi-automatic, and automatic equipment that moves the supply chain. Some of the popular material handling equipment used in the food industry are mentioned below.
Storage and handling- Racks, stacking frames, mezzanines, shelves, bins, drawers
Engineered systems- Conveyor systems, Automatic Guided Vehicles (AGVs)
Industrial trucks- Order pickers, side loaders, hand trucks, pallet trucks, walkie stackers
Bulk material handling- Conveyors, bucket elevators, hoppers, silos, stackers, reclaimers
The shift from manual to modern
Conventionally, material handling was done by human hands which had some downsides. These include injury or in grave cases, incapacitation. Human errors and mishandling are some issues that cripple food factories that do not adopt modern material handling solutions. While in some facilities, humans still perform material handling activities, they are gradually gravitating towards new technologies for enhanced productivity and worker safety.
Autonomous vehicles streamline the working of production facilities by using artificial intelligence and self-learning. This is likely to develop and continue further in the future. Floor projection lights for safety in factories are one such example already being implemented.
Robotic item picking is being used widely and has the potential to fully automate the picking process. This helps operators deal with labor shortages and cost issues. Companies are also choosing advanced gripping and vision systems that offer operational reliability to ramp up their efficiency. The central warehouse acts as the ideal location to introduce robotic item picking as technical support is available at these sites.
Warehouse control systems (WCS) are advanced control systems that act as a single-point interface to connect all other equipment and systems within their software. They connect the material handling equipment and upper-level software applications. For instance, the exchange of information between equipment like conveyors and data-rich software is made possible by WCS. This is in contrast with traditional material handling systems which were mechanical devices that moved products from one place to another.
IoT or the Internet of Things is slowly creeping into the material handling world. Systems are being built directly into equipment, and machines communicate among themselves, with little human involvement. This helps in improving the tracking, coordination, and automated data analysis. Data will be moved faster once 5G gets involved in this.
The voice recognition system is another advancement that offers reduced errors and increased productivity. In the manufacturing area, voice-picking systems facilitate communication between operators and a computer via the headset. This process is hands-free, so the operators can keep both hands on the equipment while receiving instructions from the computer, resulting in a secure working environment.
As the material handling techniques become smarter, the supply chain becomes simpler, employees’ day-to-day duties will change and the workplace will become more tech-savvy.
Big data and fuel management
In food factories, the fuel used to run the equipment is an important cost, especially for machines that run around the clock. By using the power of big data, companies can examine how much fuel is used as well as how it is being used. This pushes more fuel-efficient techniques in operations and improved operator safety. By identifying the flaws and inefficiencies, companies can improve efficiency, reduce costs, and enhance productivity.
Incorporating sustainability
Sustainability is necessary for all industries, including food. Companies are investing time, money, and effort in making their material handling systems environmentally friendly. For powering their premises, they are moving towards renewable resources. In countries like France and UK, from the year 2030, a ban on the manufacture of new diesel and engine trucks is expected to be implemented. This will be done to lower chemical emissions and improve the air quality in those regions. Further, there is an increase in demand for electric trucks and sustainable batteries like Lithium-ion batteries due to their longevity.
In today’s uncertain times when consumer purchasing behavior fluctuates unpredictably, food operators have the challenge to control their supply chain and inventory efficiently. Material handling equipment manages the inventory movement in production areas, and warehouses along with external unloading and loading. A well-designed material handling system improves customer service, reduces delivery time, and lowers inventory and overall handling costs. As the food and beverage industry gets progressively competitive each day, food manufacturers should adopt new-age material handling technologies to stay relevant.
Click HERE to subscribe to our FREE Weekly Newsletter