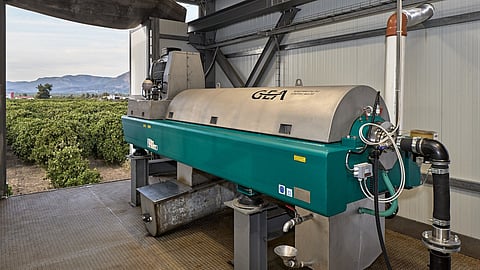
When the taste of nature meets the taste for custom-fit, individual solutions, the result can be a harmony that delights, succeeds, and fascinates. With the Greek producer of fruit juices, purees, and preparations as well as flavors and oils, Aspis, and the machine and plant manufacturer and solution provider GEA, two partners, following four-decade cooperation in the fruit juice process, have found each other to work together on an environmental project at a high technological level.
GEA, along with long-standing partner, PanMarine, planned, developed, and supported the implementation of the water and sludge treatment project at the Aspis site in Argos, Greece, a town of 22,000 inhabitants in the northeastern Peloponnese. As significant as Argos is considered to be the oldest continuously populated city in Europe, GEA's contribution is equally important for the company, which enjoys a good reputation beyond Greece as a sustainable and economically successful company.
"Our high-quality products support a large number of private labels of well-known and recognized retailers in 70 countries. Our goal is to expand our product portfolio and reach every attractive new market we have not been able to participate in," says Marios Chronis, general manager, Apsis.
GEA takes sludge processing to a new level
Delicious and refreshing citrus juices tickle the palates of many people around the world. But before the tasty drink runs down the throat, many process steps are required. This requires a lot of water, for example in the cleaning of the citrus fruits and the production of the juices. This water, as demanded by state authorities worldwide and of course also by the Greek authorities, must not simply disappear into sewers after use. It must be treated - and that is GEA's competence.
It is the hour of the GEA sludge Decanter pro 6000, a centrifuge that combines the competence from 130 years of separation expertise in one plant. The basic idea: For all types of disposals, that is, incineration, landfilling, and agricultural utilization, the optimum economic dewatering of sludge is a key step.
In practice, this means that less sludge has to be disposed of, which saves transport costs, reduces energy consumption for drying and incineration, and cuts CO2 emissions.
Therefore, curtain up for the GEA decanter. The GEA sludge Decanter ensures a high degree of dewatering with much less water consumption, resulting in a daily 50,000 liters of water savings. This is achieved, among other things, by a high g-force for optimum separation efficiency and by process-optimized torque control.
Aspis is enthusiastic about technology - but also about the other advantages
Not only the decanter technology impressed Aspis, but also GEA’s overall concept. The concept did not only include the installation of the efficient GEA decanter. GEA along with PanMarine from the early stages of this project offered an integrated solution that would fit precisely to the existing biological treatment plant. GEA's decades of experience ensured a seamless transition to dewatering by decanter technology. In the end, this total package from A to Z was a convincing argument for Aspis to engage GEA as a partner.
Water and sludge treatment - what else comes 'out' beside the water?
Now it would be quite simple if 'only' treated water came out with GEA separation technology. But even 'cash' comes out. After separation by the GEA decanters, solids are produced that can be used as fertilizer or as a raw material to produce biogas and therefore, electricity, as Aspis is doing with its partners. And the sludges can even be used to produce pellets, which in turn can be used to heat buildings. It turns out: even in residues produced by separation technologies, there are hidden opportunities for the circular economy and the meaningful use of even supposed waste.
And it works...
So, it's literally on at Aspis. And more and more companies are interested in GEA's overall competence in water and sludge treatment.
Click HERE to subscribe to our FREE Weekly Newsletter